FOCUS ON: Nearshoring
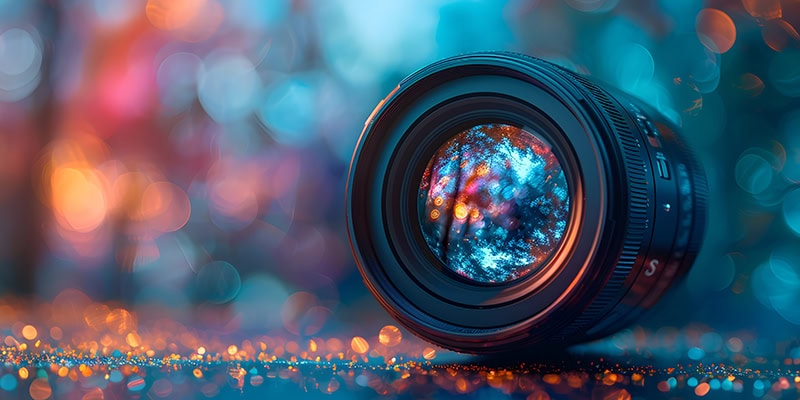
Nearshoring: Hype or Happening?
While businesses of all types are exploring the idea of reorganizing supply chains so manufacturing and production occurs closer to the United States—with the focus largely on Mexico—it’s still unclear exactly how much traction nearshoring has gained. Some experts say nearshoring is definitely here to stay, while others claim the buzzworthy practice won’t truly change the supply chain landscape:
⤊ HAPPENING
“Major supply chain trend in 2025: Reshoring and nearshoring. As geopolitical tensions and compliance regulations mount, companies will continue to shift sourcing and manufacturing away from China to other Asian countries as well as Mexico.”
–Donald Hicks, CEO & Founder, Optilogic
“Nearshoring will continue in 2025, with increasing trade restrictions focusing on domestic manufacturing and supply chains in the United States and affecting global trade partners. Transparency and supply chain assurance will be critical as new restrictions on domestic content and product origin are considered. Companies will need enhanced visibility through all supply chain tiers and mechanisms to validate component origins.”
–Michael Aller, Director, Supplier Development, FloridaMakes,
part of the MEP National Network
⤋ HYPE
“While nearshoring is often touted as the next big thing, its impact is likely overstated. We won’t see a seismic shift in 2025. Transitioning from global dependencies requires massive investment, time, and coordination that many businesses can’t quickly absorb. Even with rising tariffs and shipping-related costs, global networks still offer unmatched cost advantages and access to specialized suppliers. Companies may adopt a hybrid approach, balancing localized sourcing for some items while retaining global partnerships for scalability and economic efficiency.”
–Ed Rusch, Chief Marketing Officer, Magaya
“No tariff will bring mass production of consumer goods back to the United States in the near future. Brands offering affordable apparel and fast-moving consumer goods remain dependent on low-cost overseas production, while consumers expect cheap, abundant products. The United States currently lacks the manufacturing capacity and labor force needed to support such large-scale domestic production.”
–Sébastien Breateu, Founder and CEO, QIMA
“It is unclear what will unfold in 2025 between China and the United States. During previous geopolitical tensions between the two nations, some American companies moved their operations and inventory to other sites, such as Vietnam. However, this time, companies may be required to shift operations to the United States. This has the potential to cause some chaos in the electronic manufacturing landscape, as I am unsure how well set up the U.S. is to take on all of this production. Time will tell.”
–Kenny McGee, CEO and Founder, Component Sense
From Mexico to the U.S. Faster
Growing interest in nearshoring has prompted logistics providers to introduce new services. For one, Schneider’s new cross-border intermodal offering provides continuous rail service connecting Mexico and Texas with Florida and Georgia, as a result of a new partnership between rail providers CSX and Canadian Pacific Kansas City (CPKC).
This service aims to provide shippers with an alternative to traditional truck transportation, offering secure cross-border transit and reduced delays. Leveraging CPKC’s border-crossing infrastructure, Schneider’s intermodal solution eliminates intermediate stops, which provides quicker customs clearance and minimized exposure to theft—two key concerns for companies that have moved production to Mexico and ship goods cross-border to the United States.
In addition, Schneider’s lightweight equipment and heavy-haul permits promise added savings and increased payloads for shippers.
Mexico Beefs Up Industrial Development
Mexico is doubling down on its moves to position itself as a nearshoring hub with an ambitious plan led by the Mexican Association of Private Industrial Parks (AMPIP). Over the next six years, AMPIP aims to develop 128 new industrial parks across the country, significantly increasing Mexico’s current total of 435 parks.
These parks will be strategically located in key regions such as the Bajío, northern Mexico, and along the Pacific corridor, areas already known for their robust manufacturing and logistics sectors (see map above). This initiative seeks to attract foreign investment, strengthen supply chain resilience, and meet the growing demand for manufacturing spaces driven by companies relocating operations closer to North America, according to AMPIP.
The new industrial parks will enhance Mexico’s infrastructure and aim to solidify the country’s position as a critical link in global supply chains. With companies looking to avoid disruptions and reduce costs, these parks are poised to become a cornerstone of Mexico’s nearshoring strategy, offering state-of-the-art facilities and proximity to the U.S. market.
AMPIP’s vision aligns with Mexico’s broader economic goals, making the country a key player in the shifting dynamics of global trade and manufacturing.
Hyster-Yale Commits To Building American
As nearshoring gains momentum in reshaping supply chains and revitalizing domestic manufacturing, Hyster-Yale Materials Handling is stepping up to meet the moment. The company, maker of Hyster and Yale brand industrial trucks, has announced a strategic commitment to align with the Build America, Buy America (BABA) Act requirements. This initiative aims to bolster American manufacturing by meeting domestic production standards for electric container handling and forklift equipment used in federally funded infrastructure projects.
The company plans to expand its U.S. manufacturing operations with a focus on high-capacity electric models that cater to BABA-compliant infrastructure needs. Efforts include identifying optimal production locations, fostering domestic supplier partnerships, and enhancing the development of electric power options for its equipment lineup. In addition, the company is strengthening its partnerships with domestic suppliers and identifying optimal U.S. production sites.
Tony Salgado, chief operating officer, Hyster-Yale, emphasizes the company’s commitment to delivering innovative and durable material handling solutions: “Beyond compliance, we are evolving to better support our customers with industry-leading design, durability, and performance standards synonymous with our brands worldwide.”
Reality Check
To nearshore or not to nearshore is a question a lot of companies are asking these days. SAP recently released a best practice guide to help companies that are evaluating this question. The decision, SAP notes, should factor in switching costs, available resources, data-sharing with partners, and more.
Here are five critical realities businesses should consider when adopting nearshoring or reshoring strategies:
1. Cost savings aren’t guaranteed. While nearshoring can reduce transportation costs, factors like higher labor rates and infrastructure investment may offset savings. Companies must weigh upfront expenses against long-term operational benefits to determine true cost-effectiveness.
2. Supply chain complexity doesn’t disappear. Moving production closer doesn’t eliminate supply chain challenges like managing diverse suppliers or ensuring raw material availability. Companies must build robust local supply networks to avoid new disruptions.
3. Reshoring requires significant investment. Shifting operations back to domestic markets often demands capital for facilities, technology, and workforce training. Businesses need a clear plan for addressing these financial and operational hurdles.
4. Skilled labor shortages may persist. Finding a qualified workforce can remain an obstacle, even with reshoring. Investing in automation and employee training programs is essential to mitigate labor shortages.
5. Global risks still influence local decisions. Despite nearshoring, businesses remain affected by global market fluctuations, geopolitical tensions, and trade regulations. Maintaining a diversified strategy can help balance these risks.