Operating Regenerative Supply Chains; Tech That Attracts Workers; Cargo Theft on the Rise; and Other News
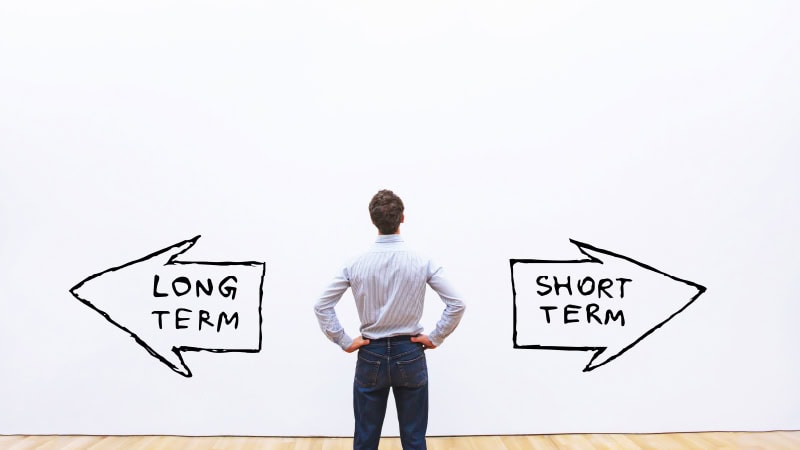
From weighing decisions that offer quick wins against those aimed at long-term gains to coping with workforce shortages, here are the latest issues and developments affecting supply chain managers.
Quick Wins Vs. Long-Term Gains
Supply chain managers frequently need to make a choice between decisions that offer quick wins and those aimed at long-term gains. Making decisions throughout the pandemic and amidst recent supply chain disruptions like the Red Sea attacks and the wars in Ukraine and the Middle East can take a toll on long-term planning.
This balancing act isn’t always easy, and only 55% of chief operating officers (COOs) feel that they are effectively operating regenerative supply chains after the past few years of turmoil, according to The Kearney COO Study 2024 from global management consulting firm Kearney and Amazon Web Services.
The second annual report is based on a survey of senior operations leaders across more than 10 industries and provides both a retrospective of the accuracy of their forecasts from last year and a look ahead to what to expect throughout 2024.
Here’s what they had to say:
2022 Forecast vs. 2023 Reality:
- 63% of COOs forecast growth of 10% to 19% in 2023; actually it averaged out at 3% to 4% globally.
- COOs singled out innovation and new products as two of the three top growth drivers for their companies; this held true, especially in the United States.
- 85% of COOs said they would make changes to their manufacturing footprint; this proved accurate, particularly in the United States.
- COOs overestimated their expected digitalization progress in every area, most notably off by 13 percentage points in sourcing and procurement and by 10 points in manufacturing.
- 66% of COOs said energy savings/renewables and climate change mitigation were top priorities in 2022; only 25% had achieved their energy consumption and efficiency goals and 19% their carbon footprint goals in 2023.
Forecast for 2024:
- More optimism about growth: 38% of COOs anticipate growth of 10% to 19%; 15% believe growth will exceed 15%.
- Belt tightening: 30% want to cut 8% or more from their expenditure; another 51% are targeting 5% to 7%; only 1% foresee cost cuts of 0% to 2%.
- Prioritizing investments with quick ROI: 7% to 10% of COOs will pursue efficiencies in maintenance and equipment effectiveness; 5% to 7% driver-based statistical forecasting; and 4% to 6% distribution optimization.
- Innovation as a joint venture: 76% of COOs are looking for joint innovation with suppliers; 87% expect this to be a key criterion in choosing suppliers; 86% said collaboration was key to operating a regenerative supply chain.
- More progress in the ‘E’ of ESG: 76% of COOs are leaning heavily on energy savings; 60% on carbon pricing mechanisms to evaluate their sustainability performance.
- A cautious approach on GenAI: 78% of these companies have invested in GenAI, but for the majority it’s for a single use case.
- Workforce of the future: 82% said labor cost was the most important factor in sourcing; 28% of COOs are concerned about their ability to upskill employees; 23% worry about the ability to retain talent; 21% worry about labor shortages.
Where Does Resiliency Reign?
If you’re looking to locate or expand your company in the world’s most resilient business atmosphere, head to Denmark.
The small Scandinavian country ranks highest on a diverse spectrum of 18 resilience factors, including logistics strength, education, and inflation, according to the 2024 FM Global Resilience Index from commercial property insurer FM Global.
The factors are sourced from a combination of respected third parties and FM Global’s vast engineering database, which draws upon data from FM Global property risk engineers who visit and assess more than 100,000 locations annually around the world. This year’s index also incorporates proprietary AI-enhanced risk modeling.
The 10 countries with the most resilient business climates are:
1. Denmark
2. Luxembourg
3. Singapore
4. Switzerland
5. Germany
6. Sweden
7. Finland
8. Norway
9. Belgium
10. Central United States (The U.S. is divided into three separately ranked regions.)
Workforce Woes: Technology to the Rescue?
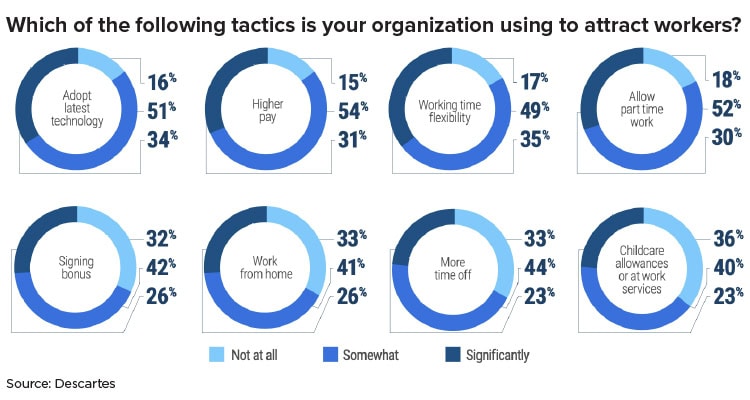
Source: Descartes
It’s no secret that supply chain operations are experiencing notable workforce shortages. A January 2024 report from logistics technology solutions provider Descartes showed 76% of survey respondents agreeing with that statement and 61% saying the problem is extreme.
So how are companies coping? And what are they planning for the future? That is the focus of Descartes’ newest survey, What Are Companies Doing to Survive the Supply Chain and Logistics Workforce Challenge?
Some 1,000 industry decision-makers responded to the survey, sharing strategies that span across technology investment and deployment, recruitment and retention, and efforts that involve external resources. Here are some key highlights:
Technology:
- 54% of supply chain and logistics leaders are focused on automating non-value-added and repetitive tasks with technology to improve worker productivity.
- Warehousing operations (40%) and transportation operations (32%) are the top areas for technology investment.
- Delivery route optimization (54%) and driver mobile productivity solutions (45%) are the top technology choices for mitigating labor shortages.
Strategy:
- 50% are co-mingling operations with other divisions to create scale and synergy.
- 40% are leveraging fleet and common carriers while 39% are co-mingling operations with other companies.
Attracting Workers:
- Working time flexibility (35%) and adopting the latest technology (34%) are top tactics for attracting workers.
- 43% are working with trade schools to attract workers, while 37% are partnering with universities.
- Immigrants (37%) are a top alternative source for workers, followed by people with disabilities (34%).
Law & Order: Warehouse Unit
Failures or errors in warehouse software can cause logistics headaches for users—and for the providers offering the technology. But in one recent case, the software snafu turned into a multi-million-dollar court case that has the supply chain sector buzzing.
Logistics company GXO Warehouse Co. (formerly XPO Logistics) was recently ordered to pay more than $33 million to chocolate maker Lindt & Sprüngli as a result of failures in a warehouse distribution software system. Lindt & Sprüngli, a major chocolatier that owns brands such as Russell Stover and Ghirardelli, brought the lawsuit against GXO due to issues occurring during Lindt’s 2014 acquisition of Russell Stover amidst efforts to consolidate warehousing for its chocolate brands.
The software failure in December 2018 and early 2019 led to what Lindt described as “massive harm” from sales losses and additional costs during the peak chocolate sales season. The jury awarded Lindt $18.3 million for lost profits and $15.1 million for extraordinary expenses after a trial in the Western District of Missouri. The case included claims of fraudulent and negligent misrepresentation, breaches of contract, and professional negligence, all of which the jury found in favor of Lindt.
“We strongly disagree with the verdict, which relates to a legacy issue from 2017 under prior management, and intend to appeal,” noted a GXO spokesperson.
Measuring the Health of Global Trade
The global supply chain got a recent check-up and the prognosis is surprisingly healthy: Q1 2024 marked the third consecutive quarter of upward momentum after a prolonged period of sluggish activity, according to Tradeshift’s Q1 Index of Global Trade Health. Spurring the diagnosis are the following data points:
- Transaction volumes across the transport and logistics sector reached their highest levels in nine months as order volumes across the manufacturing sector showed fresh signs of recovery.
- Total trade activity across the Tradeshift network improved by one point compared to the previous quarter.
- Demand signals across the manufacturing sector climbed to one point below the expected range while new orders rose at one point above expectation.
It’s not a completely clean bill of health, however. The report indicates Q1 was the ninth consecutive quarter of overall growth below expectations. Here are some key trends that impacted the wellbeing of global supply chains during Q1:
- China turnaround: Trade activity in China rose at the most significant rate in Q1. Transaction volumes grew at two points above the expected level, the highest in more than two and a half years.
- U.S. moves up a gear: The United States also continued gaining momentum in Q1, with total trade activity tracking one point above the baseline. Order volumes surged to seven points above the expected level.
- Eurozone edges higher: Activity levels across the Eurozone improved to three points below the baseline in Q1 having sunk as low as nine points below that level just six months earlier. New orders grew at six points above anticipated levels.
- UK orders disappoint: UK trade activity improved to four points below the expected level in Q1, but order volumes were sluggish, tracking five points below expectations.
Snapshot: Cargo Theft
What commodities do cargo thieves most commonly target? And from where are they usually stolen? Data in the recently published Annual Cargo Theft Report 2023 from TT Club and BSI SCREEN Intelligence answers these questions.
Last Mile Gets Flexible
With new supply chain disruptions popping up all too frequently, flexibility has become a big buzzword. It’s also widely sought after as a key to efficiently addressing last-mile delivery challenges—a new essential for brands aiming to improve efficiency and customer perception.
Flexible last-mile processes have a crucial impact on shipper revenue, loyalty, and bottom line, finds a survey of retailers in the U.S. and Canada conducted by digital insights firm Incisiv and last-mile provider Veho.
The survey also revealed that:
- Delivery choices are a must for D2C brands. 77% of brands emphasize the need for a wide range of last-mile delivery options for growth, and 81% identify two-day delivery as critical to satisfying customer expectations.
- Fast, flexible delivery options increase sales. Giving shoppers choice and control increases ecommerce conversion rates by 8.9%, and having options increases average order value by 10.6%.
- Effective last-mile strategies reduce operational costs. 92% of brands reduced operational costs by avoiding issues related to delivery mishaps, returns, and customer service.
Supply Chain-Related Bankruptcies on the Rise
We’re all familiar with the havoc wreaked by the clogged ports, long backorders, and scant raw materials supply of 2021 and 2022. While it seems like a distant memory now, some companies are still feeling the effects—all the way to bankruptcy court.
Corporate bankruptcy filings reached a 13-year peak in 2023 and are continuing at a steady pace—with many companies linking their financial troubles to pandemic-related snags in their supply chain such as the inability to acquire essential components and materials, oversupplied inventories, and labor shortages, finds a recent S&P Global Market Intelligence report.
For instance, appliance parts manufacturer Robertshaw US Holding Corp., automotive parts retailer PARTS iD Inc., and coffee trader Mercon Coffee Corp. all cited supply chain issues in recent bankruptcy petitions, according to S&P Global.
To stave off future bankruptcies brought on by supply chain disruptions, many companies are increasingly rethinking and investing in their supply chains to safeguard against potential risk events, notes the report, which singles out Target Corp. as an example. The mega retailer has been transforming its supply chain through automation, artificial intelligence, and machine learning to improve demand forecasting and inventory positioning.
“Without huge investments in stores, supply chain, and tech, there is no drive-up or order pickup, which were monumental growth drivers during COVID and today,” said Target CFO Michael Fiddelke during a March earnings call.
Should we expect the pace of supply chain-related bankruptcy filings to persist? Seems so. “Absent significant changes to wage growth and inflation that could accelerate the Fed’s rate cut timeline, the pace of U.S. corporate bankruptcies is unlikely to slow significantly before the end of the year, with disrupted supply chains remaining a key risk factor,” the report notes.
Spotlight on Sustainable Sourcing
ESG and sustainability continue to top the agendas for retail operations worldwide. What are some of the key trends and how are they impacting the retail sphere?
A new study, Retail Sourcing Report: 2024 Supply Chain Sustainability Trends, released by TradeBeyond, digs into these concerns. The report analyzes emerging ESG trends as well as regulatory shifts and the innovative practices reshaping retail sourcing.
Key highlights include:
- Corporate sustainability commitments: More than 80% of respondents intend to increase investment in environmental sustainability projects within the next year, indicating a growing prioritization of ESG goals at the executive level, particularly in the areas of renewable energy, ethical sourcing, and sustainable packaging.
- Ethical sourcing yields ROI: With ethical sourcing becoming a critical consumer expectation, brands focusing on transparency and sustainability in their supply chain are poised to build stronger trust and loyalty.
- A growing sustainability market: As companies gear up to respond to increasing consumer and legislative demand for eco-friendly products, more suppliers of sustainable materials and packaging, as well as service providers, are helping them. The global sustainability market in retail and CPG is projected to grow at a CAGR of 9.1% from 2024 to 2029.
- AI enhances ESG reporting: The integration of AI in ESG risk management is expanding, with a focus on improving the accuracy and efficiency of emissions reporting and environmental data processing.
- Sustainable fibers adoption lags: Despite the availability of sustainable alternatives to traditional fibers, the textile industry’s adoption rate is slow, signaling an opportunity for innovation and market leadership.
- Regulatory landscape tightens: ESG regulations increased by 155% over the past decade and are set to continue that pace in 2024, which sees the introduction of new sustainability disclosure requirements in the UK and a European Union crackdown on misleading product sustainability claims.