Bill of Materials (BOM): Definition, Impact, and Components
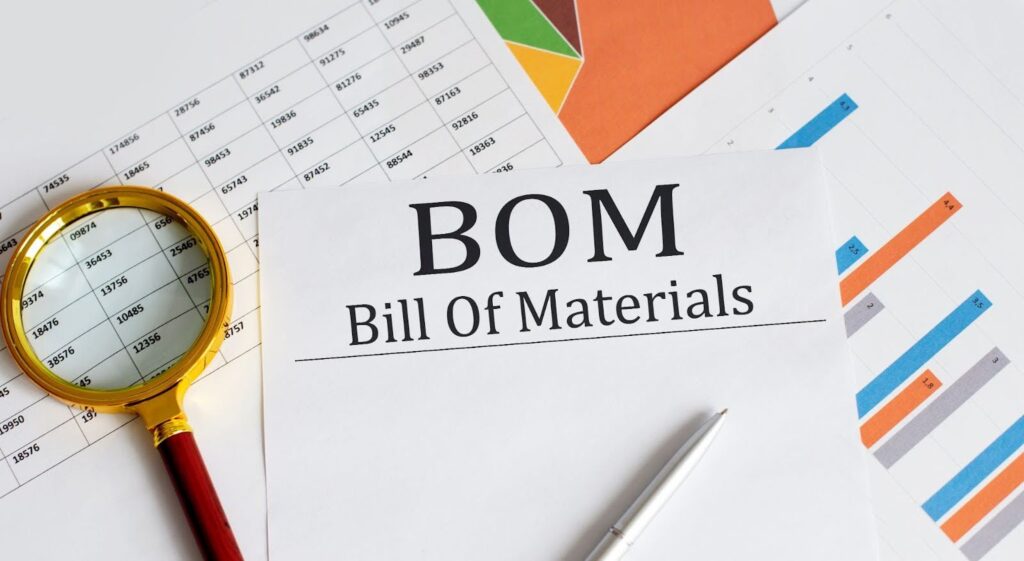
The Bill of Materials (BOM) is a cornerstone document critical to creating any tangible product in the intricate web of modern process manufacturing and product development.
It is a comprehensive list that catalogs all the components, raw materials, and assemblies needed to construct a finished product. Its accuracy and detail reflect directly on the production process’s efficiency and the supply chain’s integrity.
Consider this: a single error in a BOM can lead to significant production delays, materials shortages, or excess, highlighting its crucial role in the manufacturing process.
Definition of a Bill of Materials
A Bill of Materials, at its core, is a structured inventory of all the materials required, parts, and components necessary to build, manufacture, or repair a product or service.
The roots of the BOM can be traced back to the early days of industrial manufacturing, when the need for detailed documentation of parts became evident.
Today, BOMs have evolved with technology, incorporating software systems like Computer-Aided Design (CAD) and Product Lifecycle Management to enhance precision and collaboration across various departments.
For example, in automotive manufacturing, a Manufacturing BOM includes everything from engine components to the smallest screw, while in electronics, an Engineering BOM might detail printed circuit board assemblies.
Impact of a BOM System and How to Use One
The influence of a well-organized BOM system on a business is profound. It’s the scaffold upon which supply chain management, inventory management, and production planning rest.
Without a precise BOM, companies may struggle with materials management, leading to cost overruns or production delays.
For instance, contract manufacturers rely on detailed BOMs to ensure they have all the necessary materials and assemblies to fulfill a production order.
In the high-tech sector, data center hardware manufacturers utilize advanced ERP systems to align their BOMs with real-time inventory levels and procurement cycles.
Advantages
- Streamlines the production process by providing a detailed framework.
- Facilitates material requirements planning, ensuring materials are available when needed.
- Enhances inventory management, helping to control inventory and reduce waste.
- Improves communication across departments, from engineering to sales.
- Assists in maintaining consistent product structures for complex products.
- Enables more accurate cost estimation and production planning.
Disadvantages
- It can become complex and challenging to manage without proper software systems.
- Inaccuracies in a BOM can lead to costly production delays and materials shortages.
- Requires constant updates to reflect changes in engineering department decisions or supply chain issues.
- Dependency on BOMs can create bottlenecks if not integrated well with materials management systems.
- The complexity of multi-level BOMs may increase the chance of errors in multilevel product structures.
Components of a BOM
A detailed Bill of Materials (BOM) is a crucial navigational tool within the manufacturing process and production line, guiding teams through the intricate journey from concept to final product.
Each BOM encapsulates several layers of information, starting with BOM Level identifiers that assign a unique number to each part, simplifying the assembly and ordering processes.
A single-level BOM might list components and sub-assemblies with stark clarity. Still, a multi-level bill delves deeper, depicting a hierarchical visualization of how each part fits into the overall product structure.
Critical components of an effective BOM also include detailed part numbers, clear descriptions, and precise quantities. Additionally, a comprehensive BOM features BOM notes that convey essential instructions or comments related to the manufacturing or assembly of the product.
Raw materials, intermediate assemblies, and finished products are all meticulously documented, and procurement type is indicated to streamline purchasing actions.
Bill of Materials: Types and Examples
Understanding the various types of BOMs is significant. Each serves a unique purpose, reflecting different stages in the product lifecycle and catering to the specific needs of departments within an organization.
From engineering BOMs to sales bills, each variant holds its distinct structure, content, and application.
Engineering BOM
The Engineering BOM is a detailed documentation reflecting the product designed by the engineering department. It includes items like CAD files and design phase documents, and it’s essential for developing new products and managing product structures.
For example, an Engineering BOM for a new smartphone would list all the components required, such as the camera module, printed circuit board assemblies, and software specifications, which are critical during the design phase.
This type of BOM is distinguished from others by its focus on design phase requirements and in-depth data needed to identify parts and materials displays before manufacturing begins.
Manufacturing BOM
The Manufacturing BOM takes the Engineering BOM further by translating its technical specifications into a practical roadmap for the production floor.
It includes additional details that align with the manufacturing processes, such as assembly component lists, tools required, and materials management strategies.
Taking our smartphone example, the Manufacturing BOM would list the parts and how they are to be assembled, the assembly process, tools for each step, and production BOM notes specific to the manufacturing processes.
It is crafted to communicate the engineering design to contract manufacturers and those involved in the assembly process. The distinction lies in its practical application in the production line and ensuring materials management aligns with the engineering design.
The Engineering and Manufacturing BOMs are dynamic documents, often subject to revisions and updates as the product moves through different stages from conception to finalization.
Their accurate maintenance and updates are crucial to minimizing production delays and ensuring the materials required are always at hand. This underscores the need for robust ERP systems and materials management practices.
Sales BOM
A Sales BOM showcases the product as it is sold, including the final saleable items and the bundled items accompanying the main product. It differs from the Manufacturing BOM in that it is not primarily concerned with the assembly or manufacturing process but rather with how the product is packaged and sold.
For instance, a computer system’s Sales BOM might list the main unit, monitor, keyboard, and software, each with its code, as they appear in a sales catalog. The Sales BOM is pivotal for the sales and distribution channels to manage what end-users receive.
Single-level BOM
A Single-level BOM is a straightforward document that outlines the assembly or production of a product without detailing the relationships between the components. This type of BOM lists each part or assembly only once and does not specify the hierarchy or interrelation of parts. It is beneficial for simple products or groups where complex structures are unnecessary.
For example, a Single-level BOM for a table might list the tabletop, legs, screws, and glue without indicating the sub-assembly of the legs to the tabletop.
Multilevel BOM
Conversely, a Multilevel BOM reveals the components and the relationship between them, displaying a cascading structure of how each part fits into an assembly. It’s essential for complex products where understanding the product’s architecture is crucial.
For example, an airplane’s Multilevel BOM would detail the components of the wing assembly, which in turn would break down into smaller sub-assemblies like the flap mechanisms, all the way down to the individual screws and rivets.
Configurable BOM
A Configurable BOM caters to products customizable to customer specifications. It includes all possible variations and options that a product can have.
For example, a car model with different trim levels and optional features would have a Configurable BOM that allows the sales team to select specific configurations per the customer’s choice.
This type of BOM is different because it must be flexible and capable of creating multiple final products from a single structure.
Modular BOM
A Modular BOM supports products designed with interchangeable modules. This BOM type outlines the components and sub-assemblies within a module, which can be combined in various ways to create different product versions.
A Modular BOM is used to streamline manufacturing processes by building standardized modules rather than unique final products. An example would be a furniture series where various modules like drawers, shelves, and desks can be combined to form different office setups.
Each type of BOM serves a unique purpose within a product’s lifecycle, and the distinctions are crucial for the relevant departments. BOMs are indispensable tools in product creation and management, from facilitating sales configurations to guiding manufacturing steps.
Significance of a Proper BOM and Manufacturing
The Bill of Materials (BOM) is not just a document; it’s the backbone of the manufacturing process and supply chain management.
An accurate and well-maintained BOM ensures that every part of the production process runs smoothly, from material requirements planning to assembly. It is the blueprint from which all manufacturing BOMs derive their structure, serving as a crucial point of reference throughout the product lifecycle.
For contract manufacturers, the BOM dictates the materials template to follow, ensuring that inventory management is synchronized with production planning to meet the demands of the final product. A BOM is a strategic tool in materials management to reduce waste, improve efficiency, and control costs.
Advantages
- Fosters an organized approach to production planning and inventory management.
- It helps to reduce waste by avoiding over-ordering or under-utilizing raw materials.
- Allows for precise production order tracking and materials shortages forecasting.
- Enables the smooth integration of ERP systems into the manufacturing process.
- Assists in ensuring materials required are available, enhancing production line efficiency.
- Supports effective collaboration between the engineering department and manufacturing.
- Aids in establishing a clear production BOM, which reduces the risk of production delays.
- Enhances the capability to maintain product structures throughout the manufacturing process.
- Permits better cost estimation, leading to more competitive pricing and budgeting.
- Contributes to strategic supply chain management, allowing for quicker response to market changes.
Disadvantages
- It requires meticulous maintenance and updating, which can be resource-intensive.
- Complexity increases with the sophistication of the product structure, leading to potential errors.
- Reliance on BOM for materials management can be disrupted by supply chain volatility.
- Mistakes in the BOM can cause cascading effects, from procurement-type errors to production bottlenecks.
- Inflexible BOMs may not accommodate customizations, leading to challenges in configurable bill management.
- A BOM without integration into software systems may lead to data silos and communication gaps.
The significance of a proper BOM extends beyond just listing all the materials; it encompasses the strategic alignment of engineering bills, manufacturing processes, and supply chain dynamics.
It’s a pivotal element that translates the engineering department’s vision into manufacturing realities, ensuring that every inventory item is accounted for and every assembly BOM is followed.
For complex and multilevel BOMs, particularly for complex products, the BOM becomes even more crucial as it ensures that intermediate groups are coordinated and that the engineering BOMs align with the actual manufacturing processes.
FAQs
Delve into the intricacies of a Bill of Materials (BOM) with answers to some of the most common questions.
What is an example of a bill of materials?
An example of a BOM is the list used in building a computer, which includes the motherboard, CPU, RAM, hard drive, power supply, and case, each with detailed specifications and quantities.
What is the meaning of a bill of materials?
A BOM is a comprehensive inventory outlining all raw materials, components, and sub-assemblies required to manufacture, build, or repair a product.
What is a bill of materials for a project?
For a project, a BOM serves as a detailed list that contains all the materials required, components, tools, and instructions necessary to complete the project successfully.
Is BOM the same as COGS?
No, a BOM differs from a Cost of Goods Sold (COGS). A BOM details the materials required for production, while COGS refers to the direct costs attributable to the production of the goods sold by a company.
Bill of Materials Summary
A Bill of Materials (BOM) is the fundamental blueprint in manufacturing processes, encapsulating every necessary detail from raw materials to assembly components for creating finished products.
It underpins the entire production process, from initial production planning to final inventory management, ensuring the seamless transition of materials through various stages of creation.
By meticulously itemizing every requirement, a BOM enhances supply chain efficiency, reduces the risk of production errors, and supports the strategic management of resources, embodying the critical link between the design phase and the delivery of the final product to the consumer.