Outsourced Manufacturing: Achieving Quality and Financial Goals
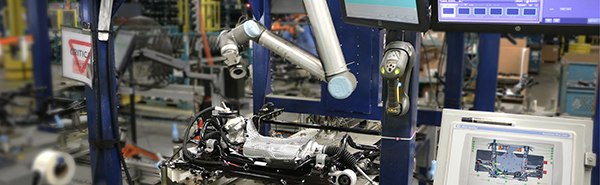
Manufacturers have been outsourcing noncore production processes for decades, and the trend continues. The key to successful outsourcing is assuring the 3PL value-added assembler (VAA) has a quality management system.
Manufacturers have been outsourcing non-core production processes for decades, and the trend continues. The key to successful outsourcing is assuring the 3PL Value-added Assembler (VAA) has a quality management system as the basis for designing and validating a robust manufacturing process.
Outsourcing supports a company’s financial and manufacturing strategies by creating floor space, increasing throughput, focusing on core high value-added activities, and driving shareholder value.
A 3PL VAA has core competencies that are complementary to the strengths of the customer. 3PL VAA provides value by leveraging competency strengths which include warehouse design and process engineering, IT systems and automation best practices, business intelligence and predictive analytics, continuous improvement culture, quality management, and financial benefit validation.
Ensuring Quality
When selecting a 3PL for value-added assembly, quality is paramount. A manufacturer’s brand, customer satisfaction, and reputation are based on producing a quality product. The outsourced 3PL VAA needs to meet and exceed the manufacturing quality goals established by the customer. A mature quality management system assures processes are planned, risk analyzed and monitored.
A world-class 3PL VAA designs around leading rather than lagging indicators. The important tools and metrics used to measure the 3PL VAA’s manufacturing quality are PFMEA and FPY (first pass yield).
PFMEA and FPY provide early prevention and detection opportunities. Root causes for a defect are pinpointed and analyzed. Corrective action is implemented and validated; error-proofing is the fail-safe mechanism used to control, and prevent, a process from producing defects.
Error-proofing (aka poka-yoke) holds the key to achieving production quality goals. Error-proofing solutions are as diverse as the failure modes that they eliminate. Examples of error-proofing include Torque Angle-Yield (TAY) system, laser distance reader, proximity sensors, witness marks, light-placement guides, robotic vision systems, and dimensional verification.
Financial Benefits
Successful outsourced relationships deliver a positive financial impact. The financial benefits of outsourced manufacturing are calculated based on the reduction or transfer of operating (variable) and overhead (fixed) expenses. Operating costs will reduce due to outsourcing.
Labor costs and wages are a major source for cost-savings and represent the largest cost-down opportunity. Headcount will be lower due to continuous improvement and engineered efficiency gains. Employee benefits, vacation, and sick time are transitioned to the 3PL VAA. The manufacturer’s corporate shared services (HR, IT, training, and quality) will then have increased capacity to focus on core activities.
Overhead (fixed) expenses such as real estate, materials handling equipment, racking, production tooling, and other costs are shifted to the 3PL VAA. An outsourcing strategy, which includes the transition of fixed expenses, will support a company’s asset-light goals, strengthen the balance sheet, increase ROIC, and provide shareholder value.
Supporting Long-Term Goals
Whether a manufacturer is considering outsourcing a single product line or a whole facility, the financial benefits have been proven.
A successful 3PL VAA utilizes their core competencies in engineering, quality management, continuous improvement, business intelligence and systems to produce defect-free assemblies. An outsourced solution supports the goals of customer satisfaction, profitability, and increased shareholder value.