Shipment Monitoring Technology: Picking Up the Signals
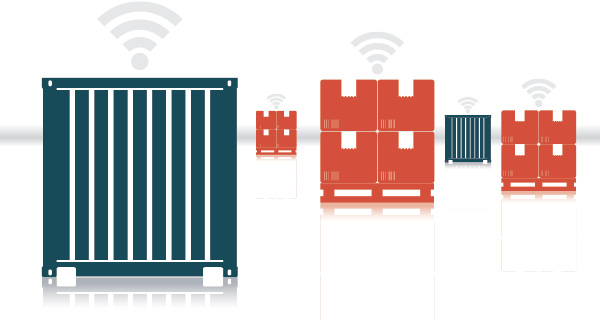
From basic to complex, tracking devices give shippers the power to locate and secure cargo at any point in the supply chain.
Shipment monitoring technology is advancing at a dizzying pace, resulting in an array of futuristic tracking devices that do everything from store solar power for five years to communicate with each other without human intervention. These advances allow manufacturers and shippers to track shipments, manage inventory, and prevent theft in previously impossible ways.
While traditional tracking devices such as radio frequency identification (RFID) and bar codes remain relevant, innovations—and dropping prices—in cellular and satellite technology make it easier to secure near-real-time coverage for almost the entire globe. Companies selecting shipment tracking technologies must balance budget constraints with a realistic view of the coverage needed.
Ultimately, knowing how to respond to the data collected matters most. Companies can turn information into action that can boost the bottom line and ensure a return on investment.
At New York City-based pharmaceutical company Pfizer, the twin goals of cargo security and inventory management guide decisions about what types of technology to use. The company employs a mix of real-time tracking devices and those offering point-to-point information, depending on the asset and route traveled.
"We don’t always use real-time data," says Bradley Elrod, director of global conveyance security for Pfizer. "Sometimes a product’s risk level doesn’t warrant the investment."
Weighing Value and Risk
The equation for selecting technology includes many variables. Shipments of materials that cargo thieves covet—such as painkillers with a high street value—might be equipped with the most sophisticated technology, such as satellite tracking devices, while drugs with a lower risk of theft or product damage are tracked less intensely. Likewise, Pfizer keeps a closer eye on shipments moving through high-risk regions such as Mexico and South Africa than calmer areas.
In situations calling for the highest levels of security, the options have never been more sophisticated. Emerging capabilities in satellite and cellular technology have resulted in increased coverage, reduced costs, and expanded product offerings.
Satellite tracking systems now generate close to real-time, location-based data across up to 98 percent of the globe traversed commercially, says Craig Montgomery, senior vice president, marketing and product management for Orbcomm, a Rochelle Park, N.J.-based provider of machine-to-machine (M2M) equipment. M2M allows separate pieces of equipment to communicate through wireless or wired networks, frequently without human intervention.
Typically, these devices allow what is called bi-directional communication. In one direction, satellites track remote assets, reporting information to a database accessible through a Software-as-a-Service (SaaS) solution. These systems are frequently cloud-based, so they can be tapped from any device with an Internet connection.
Tracking is near-real-time, although some areas experience lags, or latency, in data reporting. Latency lasts anywhere from a few seconds to several minutes, depending on how many satellites cover the asset’s location. In areas where there are fewer satellites—at the poles, for instance—data reporting is slower.
Meanwhile, M2M also allows shippers tracking cargo to communicate with the devices, changing reporting frequencies and investigating alerts generated by attached sensors. These devices can automatically switch from cellular to satellite using sophisticated software that monitors the available networks, and chooses the best system based on coverage and cost.
Cellular, like satellite, offers real-time data. It is cheaper than satellite, but covers less of the world. While its low cost can make it a good solution for tracking cargo traveling through the increasing swaths of the world covered by cellular, satellite remains the go-to option in remote parts of the world, or for assets that move in and out of cellular coverage.
Each technology offers distinct benefits, but companies have historically needed two separate devices to use both. That requirement is changing. Technological advances have reduced the footprint of communications equipment, making it possible to fit cellular and satellite components into one device, which keeps equipment costs down.
Costs have also dropped on the communication side, making the dual-mode device a more viable option.
Meanwhile, bi-reporting capabilities mean companies can switch how frequently the device generates reports. Location information for shipments traveling on a U.S. highway might report once each day. On a ship, reporting might slow to once each week—but if cargo enters a theft hotspot, updates could arrive every 15 minutes.
Theft-Prevention Measures
In addition to location tracking, M2M offers measures to tighten cargo security. Locking devices not only track cargo, but also sound an alarm if someone cuts the bolt. The devices run on ZigBee, a wireless communication system that uses radio waves to link M2M technology.
One security option wireless technology offers is creating a "slave/master" mentality. "Place several devices into pallets, and they will communicate with each other," Montgomery explains. "The pallet devices also communicate with both the master tracking device outside the pallet, and the cellular-enabled bolt mechanism."
Companies track the data—which appears on a map application such as Google Maps—in a SaaS program offered by their technology provider, or through their own software system. "They are able to see the shipment’s location," Montgomery says. "Shippers can access different perspectives, such as a satellite view of the land and ground schematics, or view a road-based traditional map."
Companies can run queries to gather information about device location, asset idles, and cargo loading status.
Battery technology has improved, too, with solar-powered global positioning system (GPS) M2M tracking devices now available. One of Orbcomm’s devices measures just one inch high, and is thin enough to fit in the ridge of a cargo container. The device—which offers near-real-time shipment visibility and the ability to change reporting frequencies—features a battery that runs up to five years in total darkness.
Conditions Awareness
Sensors that detect light and temperature, in addition to communicating real-time location data on cellular networks, mark another frontier. The ability to detect light is an important security feature, with the sensors reporting if a package has been opened prior to delivery. If a breach occurs, shippers quickly receive an email notification, allowing them to act promptly.
"When trouble hits the supply chain, shippers need to react immediately—not in a few hours," says Chris Swearingen, marketing manager for SenseAware, a FedEx subsidiary that operates a sensor-based logistics program. "This speed is especially important for international shipments, because it is easier to lose visibility."
The sensors enhance security by working with two types of geofences: route-based and time-based. This capability gives companies the option to set durations for each leg of the journey.
"If a shipment does not meet the specific time measurement for that part of the trip, it could indicate theft or another problem with transportation," Swearingen says. In both cases, shippers receive near-real-time alerts via email if a shipment breaks the geofencing parameters.
Sensor-based technology is relatively new. SenseAware launched in 2009, and is now available in 20 countries, including the United States, Canada, Scandinavia, much of Europe, and parts of Asia. Companies purchase a subscription that includes equipment, connectivity, and access to the software system through which users can track shipments.
The program builds on the Internet of Things (IoT) concept commonly referenced among supply chain technology experts. In practice, IoT refers to the rising number of physical objects traceable through the Internet. IoT posits that one day, all objects will be traceable through the Web, and able to communicate with each other.
Mobile on the Move
Mobile phones comprise part of the IoT philosophy, with new possibilities emerging—particularly with apps, says Doug Litten, supply chain IT program director for Leidos, a Reston, Va.-based technology consulting firm.
Leidos is working with mobile apps that allow employees to input cargo-related data. The app then pushes data into a central database, viewable by other authorized parties. Litten predicts the use of mobile devices in logistics will increase during the next few years, although related security and encryption still need improvement.
Even with sophisticated technology available to provide visibility, older technologies such as RFID—first developed in the 1940s—is still relevant today.
"RFID is wonderful technology," says Tom O’Boyle, director of RFID for Barcoding Inc., a Baltimore, Md.-based provider of RFID, bar-code, and wireless technologies. "It allows us to identify an item without having a direct line of sight."
When a cargo container or pallet tagged with RFID moves through a "read zone"—a portal equipped with a special reader—the reader captures the tag’s information using radio frequencies. Away from reader locations, another technology, such as satellite or cellular, must provide coverage.
While passive RFID has no internal source of power—essentially falling asleep when not activated by the reader—a battery powers active RFID. The active version’s radio frequencies communicate at longer distances than the passive version, and, in some cases, it can initiate communication with readers or other tags. Passive RFID costs less and remains more widely used than active RFID—particularly for high-volume, low-risk cargo.
Because passive RFID only works when in close range to a reader, it is often categorized as a solution best suited for warehouse management. The frequencies for either type aren’t widely standardized save for select industries, which has also limited its use.
"A business can’t necessarily use an RFID tag that has been encoded for Company A in Company B’s system, unless it has access to the database that identifies what the tag means," O’Boyle says.
Some businesses avoid RFID, considering the technology redundant if used in conjunction with more sophisticated solutions, such as GPS.
One such company is A. Duie Pyle, a West Chester, Pa.-based less-than-truckload carrier that offers tracking standard with all loads, but forgoes RFID. Instead, the carrier uses bar codes coupled with GPS systems that track trucks in five-minute intervals.
The mix provides all the data the carrier needs, and RFID would be an unnecessary expense, says Mike Crowley, the carrier’s chief information officer.
Despite its drawbacks, dropping RFID prices lead O’Boyle to predict a 30-percent surge in the companies using it over the next five years. While passive RFID tags cost 50 cents or more a few years ago, prices today are as low as 15 cents. RFID reader price tags have also dropped about 30 percent over the past few years. Lower prices may spur more users to adopt RFID, which will lower prices even further.
RFID technology continues to evolve, offering new uses. Some companies, for example, are beginning to use RFID in container seals. "Not only will we know that the seal has been broken, but a date and time stamp recording reveals when it was broken," O’Boyle says. Users can also program the technology to limit who has the authority to access containers.
No matter how far other technologies advance, RFID will remain relevant, because its low cost and accessibility make it a good option for many circumstances.
Likewise, bar codes, perhaps one of the simplest tracking mechanisms, are expected to retain their place among more sophisticated technologies. "Most supply chains are not fully RFID-capable, so bar codes are especially important for capturing data, particularly at the unit level," Litten says. "Bar codes are inexpensive, and they do the job."
Each type of tracking technology offers a specific use. While a cargo container might be outfitted with GPS, RFID more effectively tracks units or pallets. "RFID is more cost-effective than active GPS-type tags, because they cost a few cents instead of hundreds of dollars," O’Boyle says.
No More Than is Needed
Depending on a company’s needs, real-time data provided by GPS may not even be necessary.
Companies frequently think they need more visibility than they actually do. While hourly updates might seem like a good idea, point-to-point may suffice. "When businesses review customer needs, they often determine a daily location is adequate," Litten says.
Visibility requirements may vary depending upon why a company needs to know where its assets are. Needing up-to-date information from a financial reporting perspective or because the location of inventory drives procurement decisions, for example, might compel a company to invest in a comprehensive—and expensive—solution such as satellite.
Shippers should pay for the visibility they need today, keeping in mind that more detail is always available. For many companies, daily updates received through email, or by accessing a software system, represent a vast improvement on calling carriers, searching for cargo, and relying on data that might not even be accurate.
With so much data potentially available, companies must focus on making the best use of the information.
"It’s not just a question of knowing the shipment location, but also considering how that status impacts the business," says Kim Le, director of CargoSmart North America, a Hong Kong-based SaaS shipping and logistics company.
CargoSmart tracks information from its network of more than 30 ocean carriers and more than 22,000 groups of customers—called groups because each involves the customer and its supply chain partners. The company analyzes data such as carrier schedules uploaded by parties in its network; weather reports; historical information; and even news events, such as whether workers at a particular port are striking, which could delay shipments.
"Everybody in the market has data after the fact," Le says. Truly meaningful data identifies events while they’re happening, and allows companies to change routes or find other solutions to mitigate delays.
"Shippers can’t change their supply chain unless they have enough lead time to make a difference," Le says.
For example, in the case of a company whose vessels were rerouted from Long Beach, Calif., to Mexico, learning of the change early was critical. "We saw that shift, and alerted the shipper," Le says. "The company was immediately able to arrange trucks to meet the ship in Mexico and avert delays."
Increasing data availability is also changing how companies manage shipments. Information supplies the power to manage by exception—building rules, enforced by technology.
"Businesses can choose to be alerted if a certain asset or device hasn’t reported in a specified amount of time, or reports from a location where it should not be," says Lee Lanucha, senior director of platform product management at Numerex, an Atlanta-based M2M provider.
Using data, companies establish trends and prohibit actions deviating from the norm. This enhances security, and reduces staff time spent tracking assets.
"In the past, reports might come in every 15 minutes stating that all conditions were stable," says Orbcomm’s Montgomery. "But that eats up a lot of time and resources for dispatchers, who only need to know if the shipment goes off the intended path."
Technology not only provides fast, precise coordinates for latitude and longitude, but it also provides rapid communication with law enforcement authorities in case of theft. "They can catch the thieves, and get the materials back," Montgomery says.
Start Small
The array of available shipment tracking possibilities might seem daunting. When examining options, it helps to establish specific goals. "Some companies implement big, cumbersome systems that are too complex to manage," says O’Boyle. He recommends businesses start small, experimenting with a portion of their supply chain and expanding from there.
Another decision involves whether to purchase equipment outright, or work with a solutions provider. Each method offers benefits. Companies that purchase technology can place it in cargo without even notifying the carrier, which can boost security.
Alternatively, when working with a technology provider, companies needn’t worry about investing in upgrades. "The technology changes fast—what you use today could be outdated in two years," Elrod says. Companies that make large capital expenditures for equipment are less likely to invest again a few years later.
Despite all the advances, no matter how sophisticated the solution, no perfect tracking technology exists. Companies should continue to expect some holes in their tracking. "It would be nice if full visibility was possible 24/7," says Lanucha. "But all technology has some limitations."
Despite those limitations, every step toward better supply chain visibility is a step in the right direction.