Articles
Inventory Management
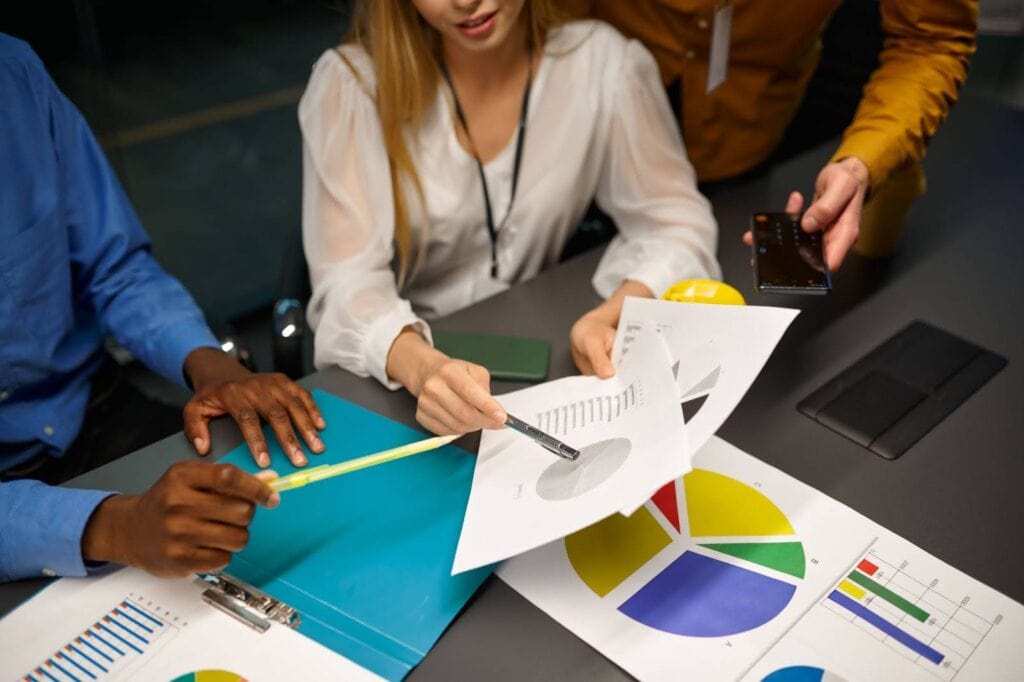
ABC Analysis: Definition, Importance, and Implementation
ABC analysis stands out as a fundamental approach in managing inventories effectively. By categorizing the total inventory items into three groups—A, B, and C—based on their value and consumption rates, businesses can prioritize their resources and focus on the most impactful items. This guide explores the intricacies of ABC analysis, providing a comprehensive understanding […]
Read More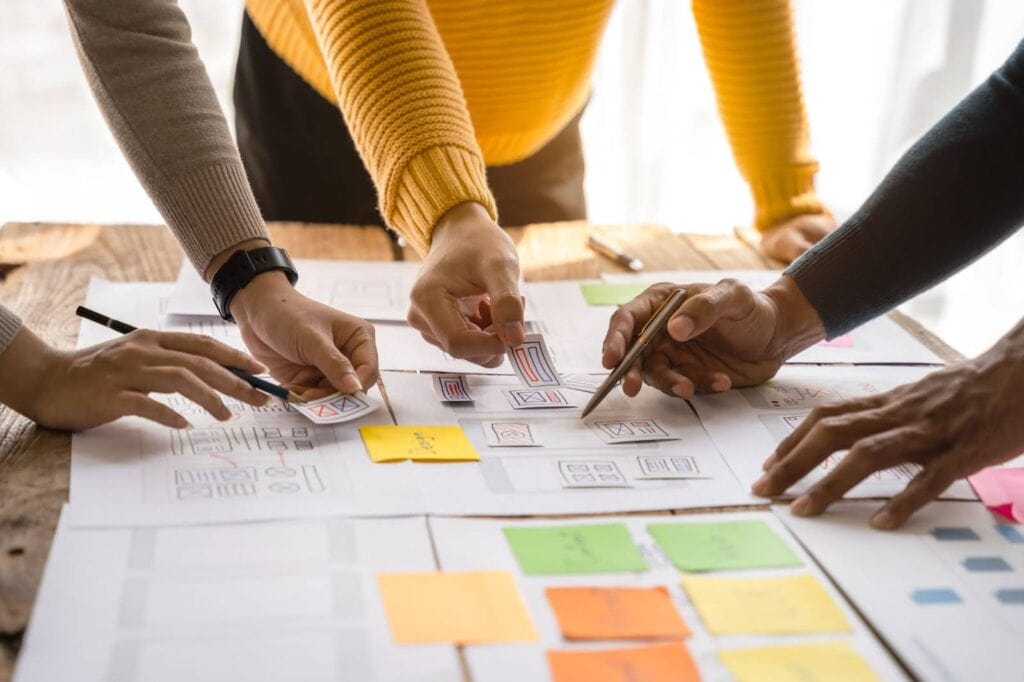
What is MRP? History, Definition, and How it Works
Running a manufacturing process without an organized system often leads to chaos—too many raw materials or not enough to meet customer demand. That’s where material requirements planning (MRP) comes in. So, what is MRP? It’s a planning system that helps production managers calculate the materials needed, schedule production efficiently, and balance inventory levels with actual […]
Read More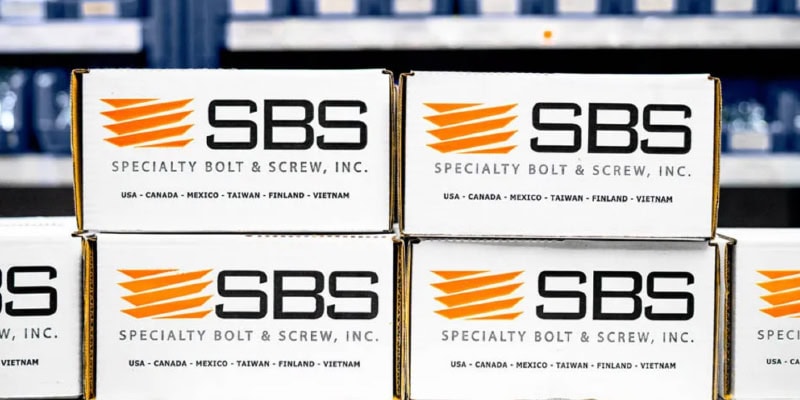
Bolting Ahead: Specialty Bolt & Screw Tightens its Supply Chain
Specialty Bolt & Screw, Inc. (SBS), a leading provider of fastening solutions, offers more than 15,000 SKUs across 12 locations, and manages a complex global supply chain. As a result, it required a more efficient and accurate inventory management and forecast function than it was able to achieve with its older, homegrown system.
Read More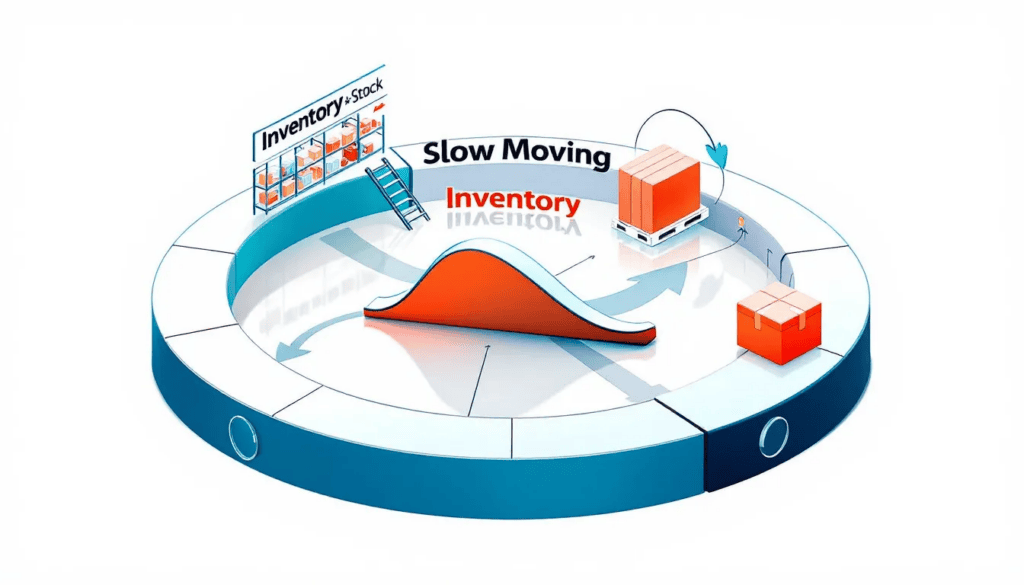
Understanding Slow Moving Inventory Definition: Identify and Manage Your Stock Efficiently
Understanding and managing slow-moving inventory is crucial for maintaining a healthy and efficient inventory system. By identifying the causes, using key metrics for identification, and implementing effective management and preventive strategies, businesses can turn their slow-moving stock into a streamlined asset.
Read More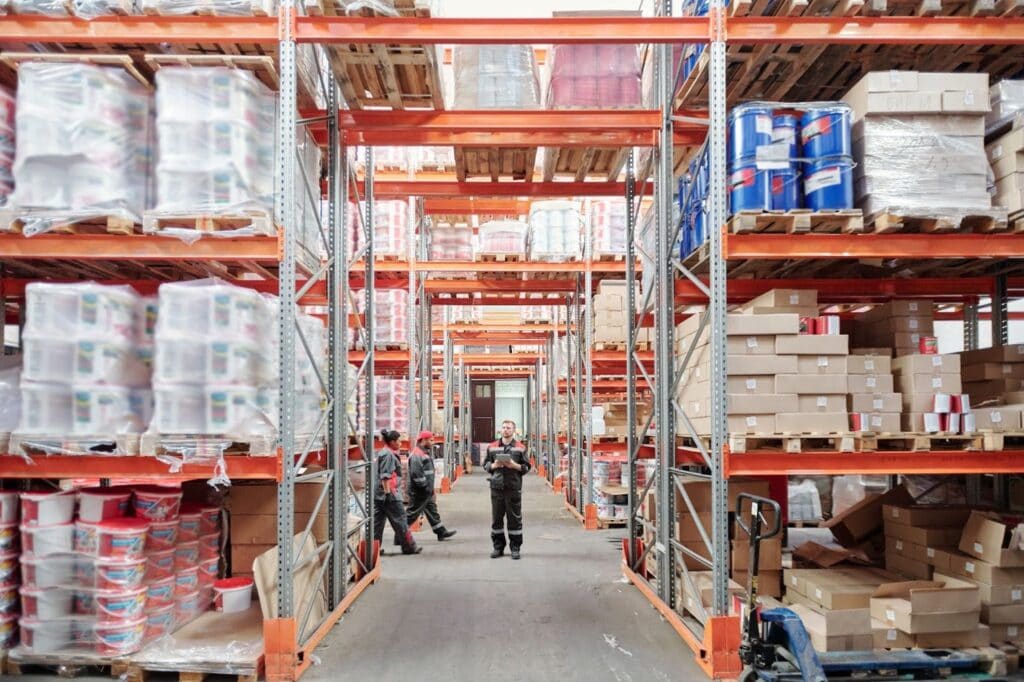
Just-In-Time Inventory: Definition, Advantages, Disadvantages
Just-In-Time inventory, or JIT, is a strategy that streamlines a business’s inventory and improves efficiency by receiving goods only as they are needed and minimizing inventory costs. This method helps maintain a lean inventory, significantly enhances cash flow, and reduces waste. In this guide, we will extensively review the JIT inventory system, exploring its core […]
Read More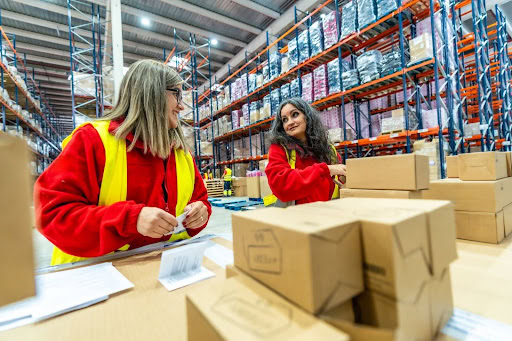
MOQ Meaning: Its Formula, and How To Optimize It
Minimum Order Quantity (MOQ): Meaning, Formula, and How To Optimize It Minimum Order Quantity (MOQ) represents the smallest amount of a product a supplier is willing to sell at one time. Businesses commonly use minimum order quantities to streamline production processes, manage costs, and meet operational demands. Understanding MOQs ensures better planning and efficient inventory […]
Read More
Warehouse vs. Inventory: Their Roles And Differences
Understanding the crucial differences between warehouses and inventory is essential for operational excellence in supply chain logistics. This article explores the roles and connections between warehouse capacities, inventory management, and their impact on inventory and warehouse operations in enhancing overall supply chain efficiency. Understanding Inventory Management Definition and Key Concepts Warehouse management is the […]
Read More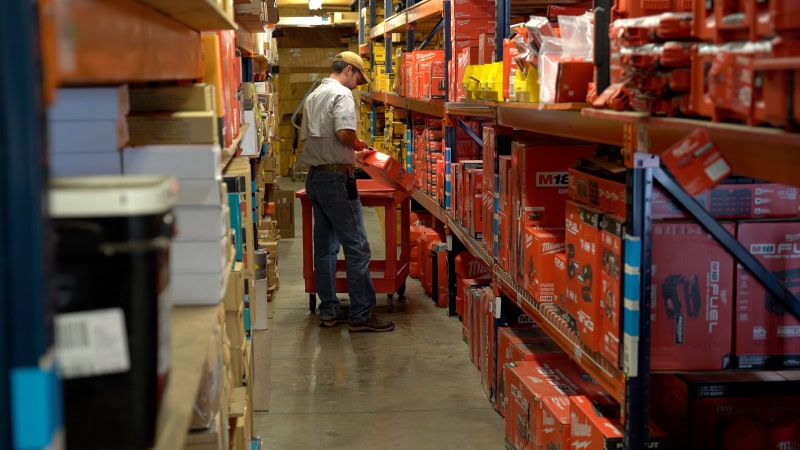
VAI and Kinnunen: Constructing Efficient Inventory Management
Kinnunen, a family-owned business that offers a range of construction supplies—from air compressors to wood glue—has enjoyed so much growth that its enterprise resource planning (ERP) system was struggling to keep up. This hindered the company’s ability to effectively manage inventory and serve customers.
Read More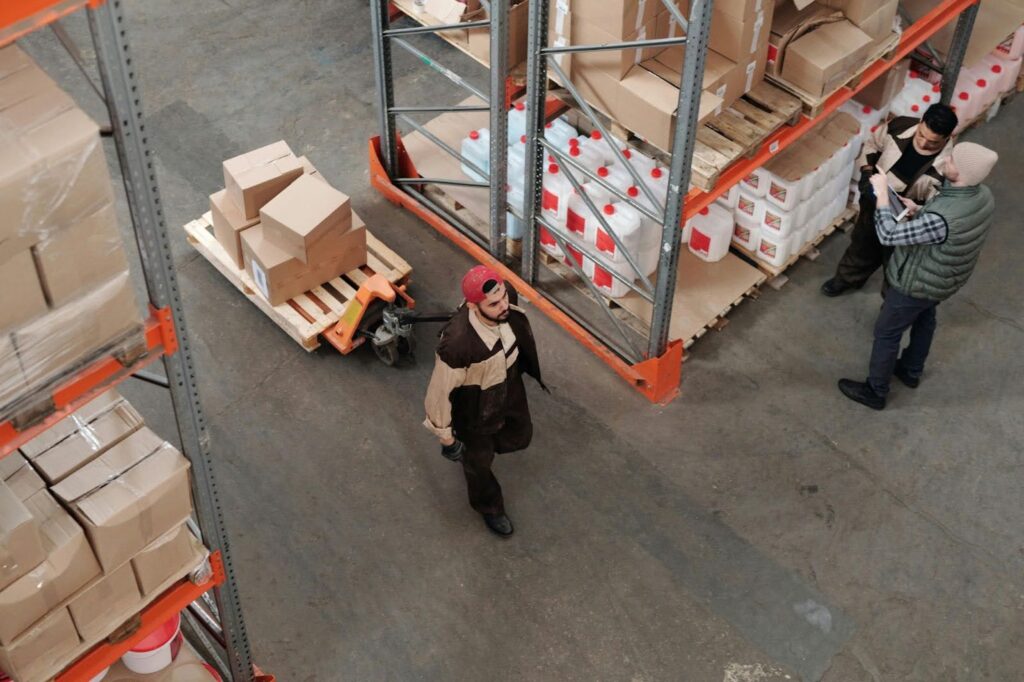
Work in Progress (WIP) Inventory: Definition, Importance, and Calculations
Understanding and managing work in progress inventory is essential for keeping your production process efficient and reducing manufacturing costs.
Read More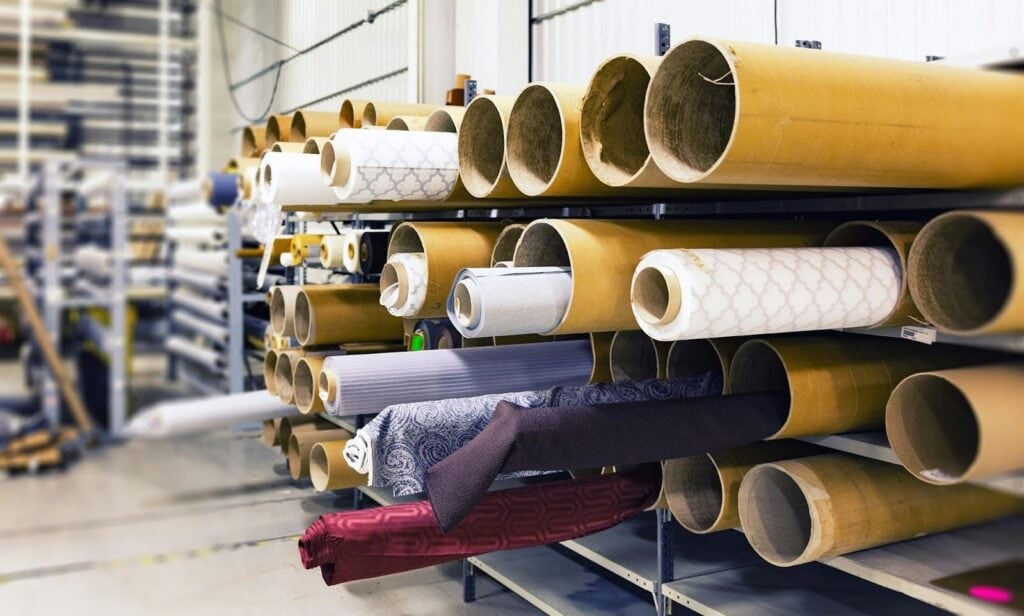
Raw Materials Inventory: Explanation, Benefits, and Tips
Understanding how to manage raw materials inventory is crucial for smooth business operations. By implementing best practices like regular audits, using software, and improving inventory turnover, businesses can control costs and optimize their production process.
Read More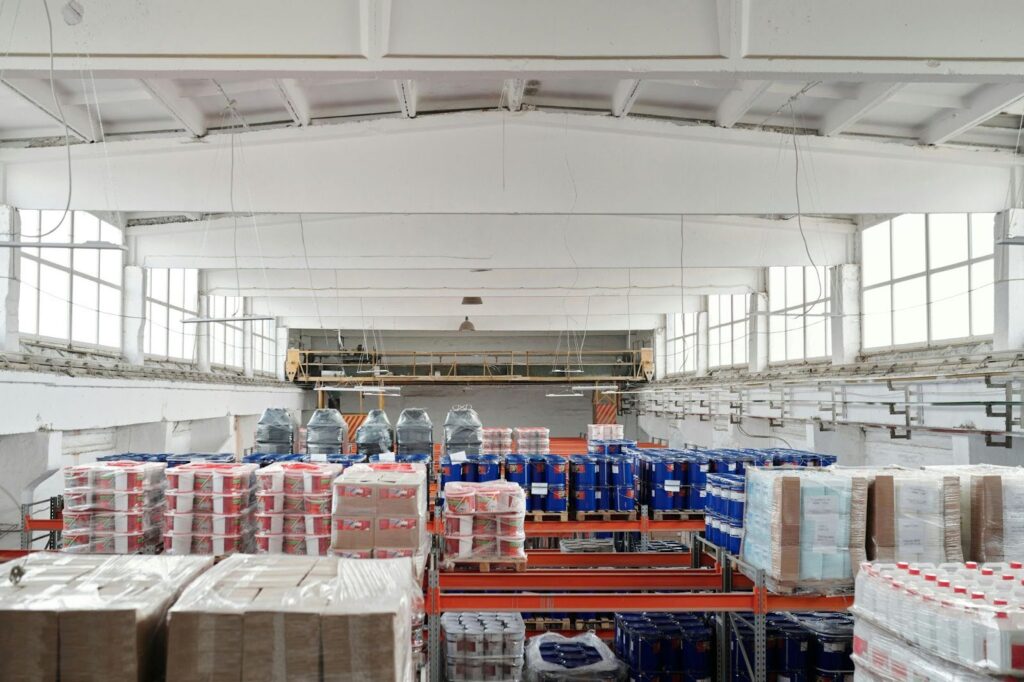
Decoupling Inventory: Definition and How It Protects the Supply Chain
In today’s complex logistics and inventory management world, maintaining a resilient and efficient supply chain is more crucial than ever. One key strategy businesses employ to safeguard against disruptions is decoupling inventory. This approach helps prevent inventory shortages and ensures customer demand is consistently met. Decoupling inventory is essential for anyone involved in manufacturing processes, […]
Read More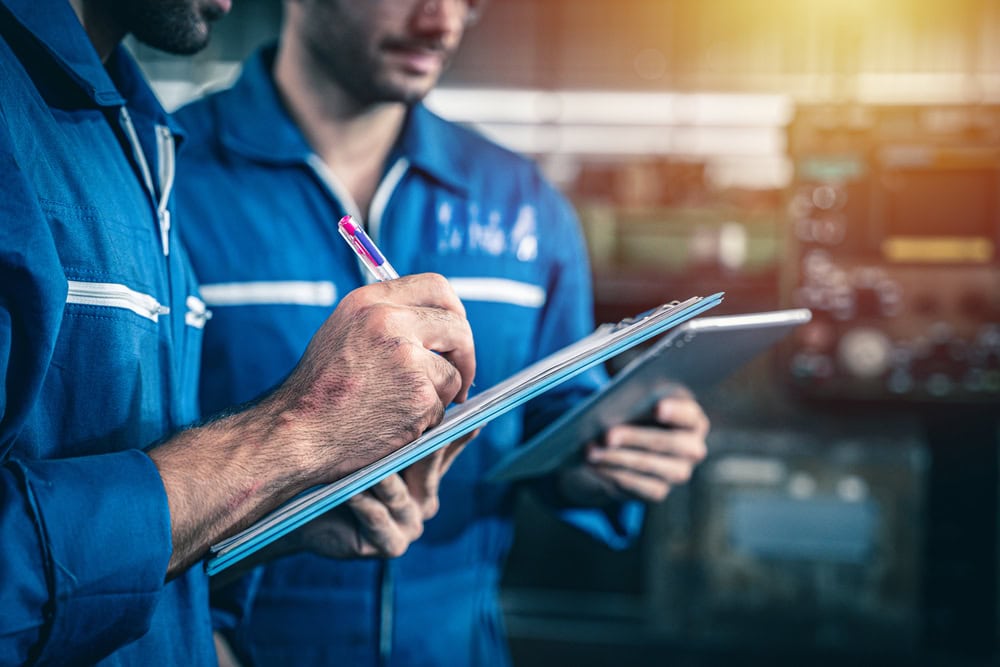
MRO Inventory: Definition, Strategies, and Types
By comprehending the definition, types, and significance of MRO inventory, as well as implementing best practices in inventory management, businesses can optimize their supply chains and ensure smooth operations.
Read More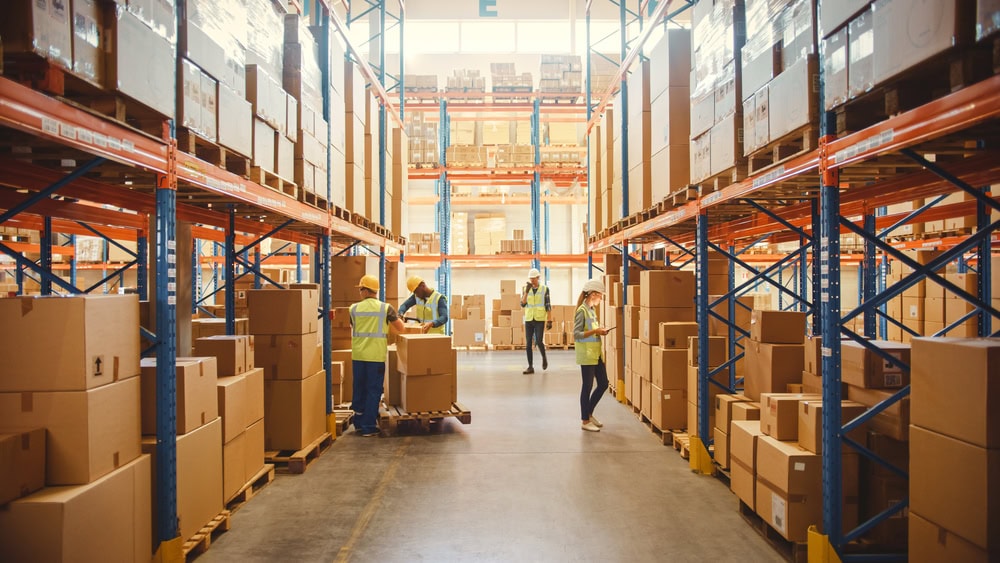
Distributed Inventory: Definition, Management Strategies, and Benefits
Distributed inventory is a strategy for storing goods across multiple locations rather than in a single central warehouse. This approach is important in commercial shipping and logistics because it helps companies align inventory with market demand and significantly cuts delivery times. By distributing inventory, businesses can achieve greater flexibility and responsiveness, enhancing overall supply chain […]
Read More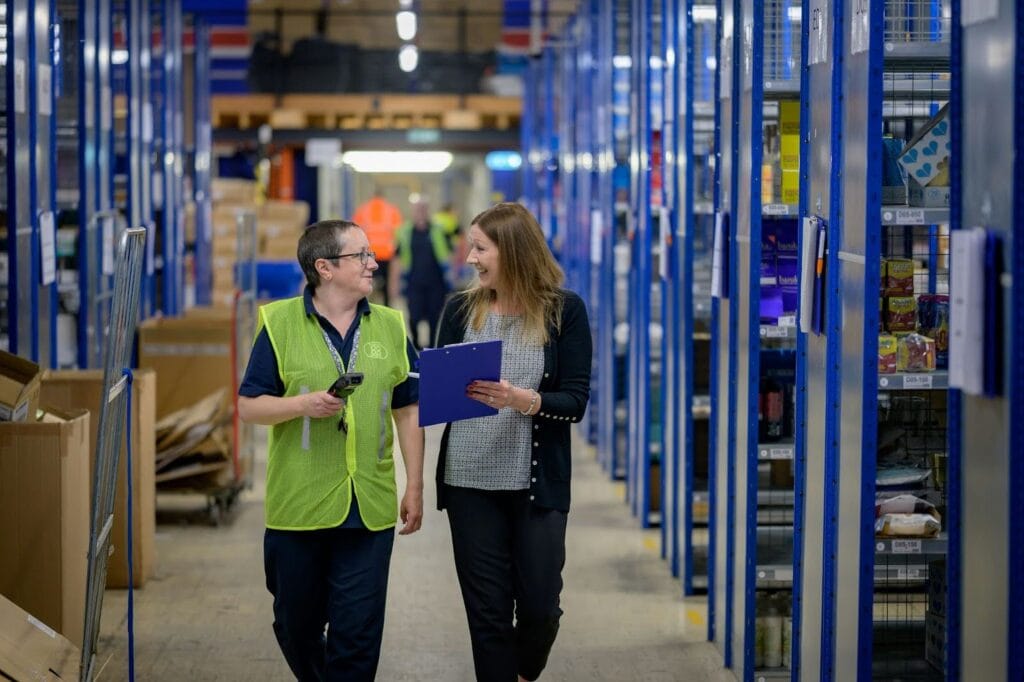
Finished Goods Inventory: What It Is, Formula, and Examples
Finished goods inventory is a critical part of managing any manufacturing business. It refers to the final products ready for sale after the manufacturing process is complete. Efficiently managing this inventory helps companies meet customer demand, optimize stock levels, and avoid lost sales opportunities. Businesses that actively manage their finished goods inventory can reduce excess […]
Read More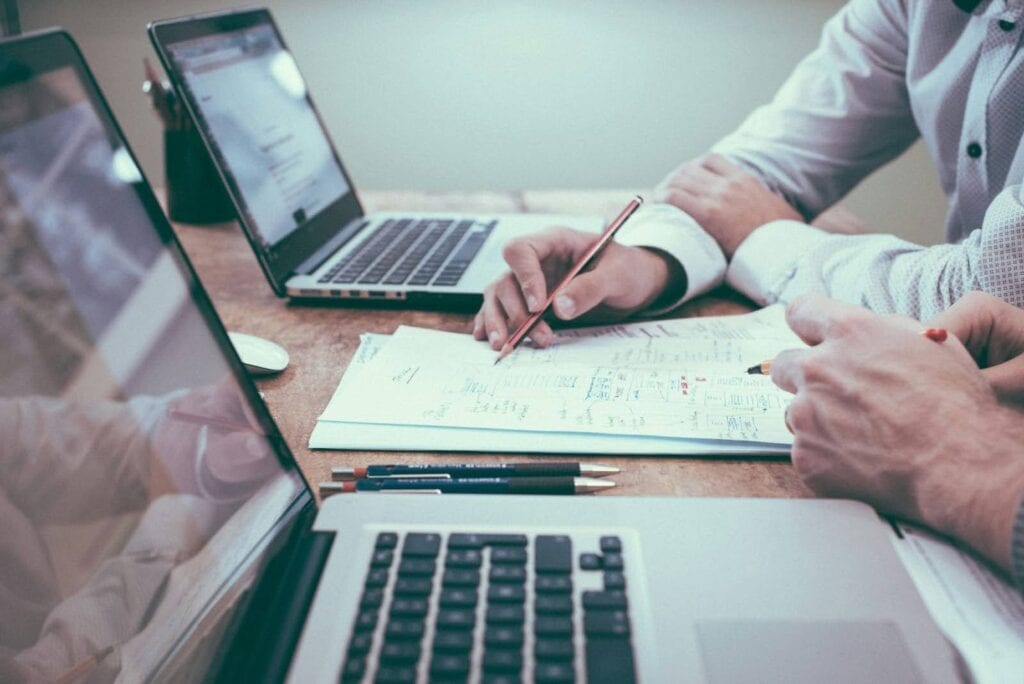
Inventory Management Techniques And Their Benefits
Each effective inventory management technique is crucial for helping a business maintain smooth operations and meet changing customer demands. By implementing inventory management strategies, companies can optimize their inventory management process, avoiding stockouts or overstocking.
Read More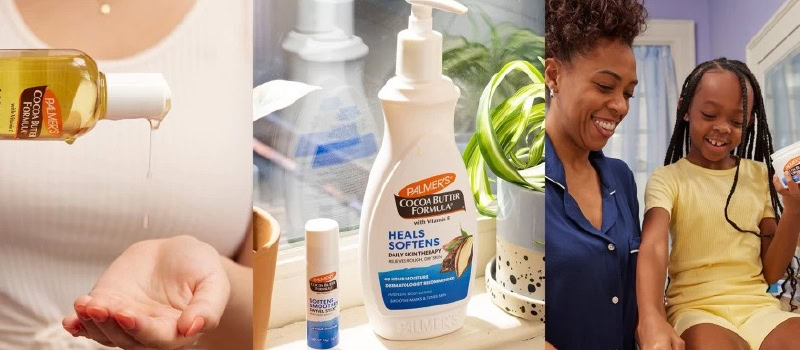
New ERP Smooths the Way for Skin Care Company
After an exhaustive review of its enterprise resource planning (ERP) system, E.T. Browne Drug Company, the maker of Palmer’s Cocoa Butter, understood it needed to upgrade. By recommitting to SYSPRO, its long-time ERP provider, E.T. Browne was able to leverage a scalable solution that has enabled the venerable skin care company to reduce inventory and grow profits.
Read More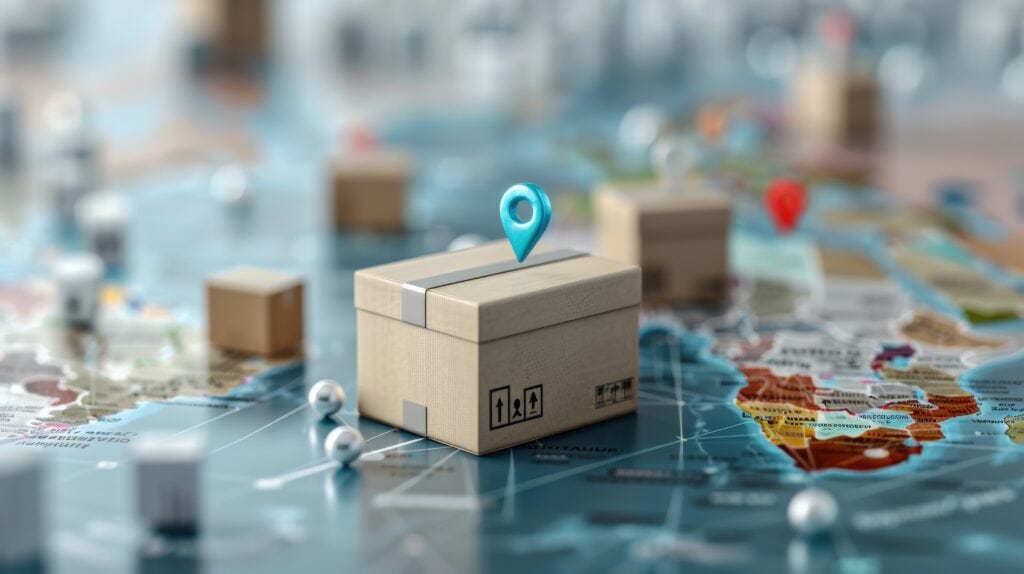
Pipeline Inventory: How To Manage It and Why It’s Important
Pipeline inventory plays a crucial role in the smooth operation of businesses across various industries. Simply put, it refers to the goods that are in transit between the manufacturer, distributor, or retailer and are not yet available for sale. Properly managing this type of inventory is essential for maintaining efficient supply chains, reducing costs, and […]
Read More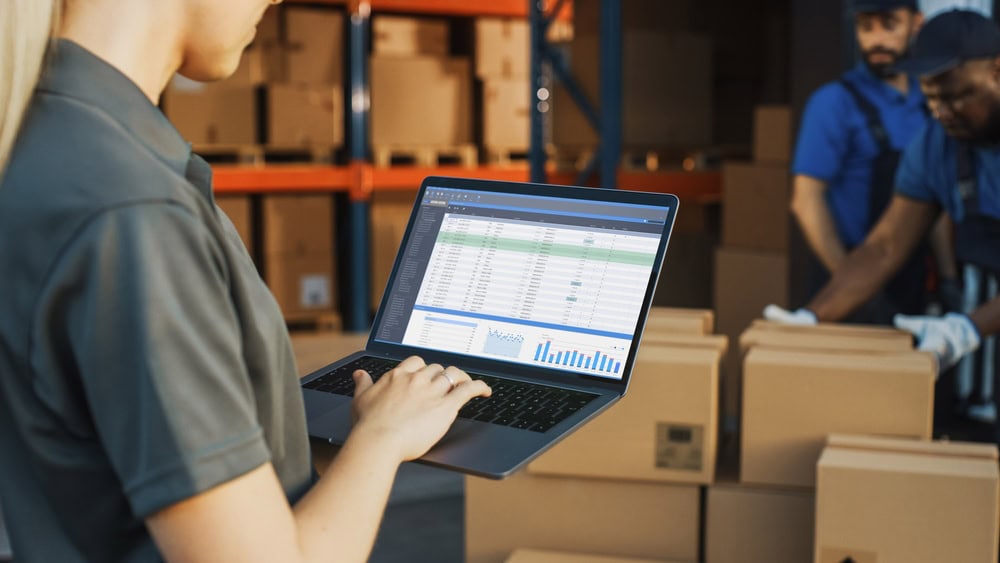
Vendor Managed Inventory: Definition, Benefits, and Challenges
Reflecting on the strategic benefits of VMI and staying informed about future trends can help companies achieve greater efficiency and success in their supply chain operations.
Read More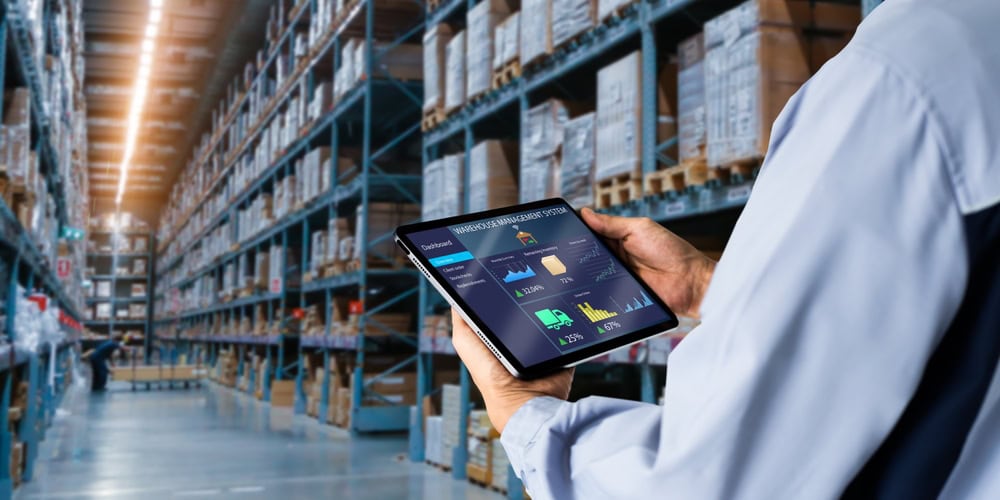
Inventory Cycle Counting: Definition, Benefits, and How-To
Cycle counting is a crucial method in inventory management that helps businesses maintain accurate records without halting their daily operations. Unlike traditional physical inventory counts, which can be disruptive and infrequent, cycle counting involves regularly auditing small portions of inventory. The main advantage of cycle counting over traditional physical counts is its ability to provide […]
Read More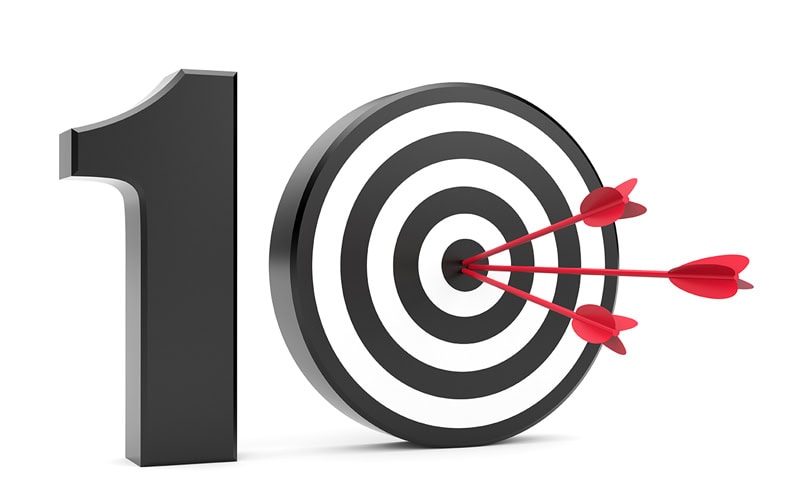
10 Tips for Managing Inventory Effectively
Effective inventory management starts with a proactive philosophy. Here are 10 steps to take that can help you improve accuracy, increase efficiency, and control costs.
Read More